Reducing Energy Use in the Food Industry: A Finance Director’s Perspective
- Chris Gunn
- Mar 20
- 2 min read
Updated: Mar 21
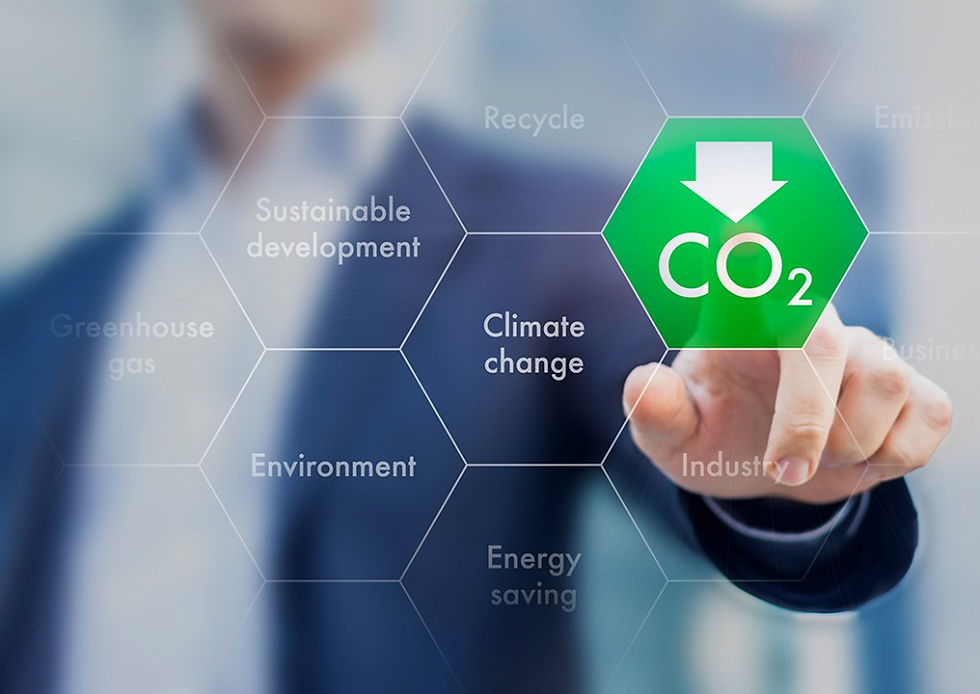
Energy costs are biting harder than ever.
For finance directors in the food industry, it’s not just an operational concern—it’s a direct hit to margins. Energy is one of the largest controllable expenses, so every unit saved goes straight back into your bottom line. But here’s the question: are we doing enough to reduce waste and rethink how energy is used?
Let’s talk about where the opportunities lie, what barriers hold us back, and why rethinking energy is not just about cost—it’s about resilience.
What’s Driving the Need for Change?
Energy efficiency isn’t just a buzzword—it’s a necessity. With soaring energy prices and growing pressure to achieve sustainability targets, every watt saved matters.
What’s really at stake?
Profitability: Spiralling energy costs chip away at already tight profit margins.
Consumer Pressure: Shoppers expect companies to walk the talk when it comes to sustainability. A commitment to energy efficiency can strengthen your reputation.
Compliance: Regulations around carbon emissions are getting tougher. Staying ahead of the curve can save costly penalties later.
With these factors stacking up, inaction is no longer an option.
Where Are You Losing Energy—and Money?
A recent study showed that up to 20% of energy use in food manufacturing is wasted through inefficiency. That’s tens of thousands of pounds lost every year.
Take a look at your operations:
Are your refrigeration systems working harder than they need to?
Does your production line operate efficiently, or are there hidden energy drains during off-peak hours?
Are you relying on outdated equipment or processes that guzzle energy unnecessarily?
These questions can seem small, but answering them honestly might uncover expensive habits that are costing more than you think.
Turning Talk into Action
The good news? You don’t need to overhaul your entire operation to see results. Small, manageable steps can deliver real change:
Data Is Your Best Friend: Energy audits can help you spot inefficiencies you didn’t even realise were there. Metering systems paired with analytics tools can identify waste in real-time.
Optimise Maintenance: Poorly maintained machinery uses more energy. Routine servicing is a quick win to increase efficiency without a hefty upfront cost.
Employee Training: The people on the floor are key. By embedding energy-saving habits, like proper equipment shutdowns, you can make improvements without major investments.
Invest in Smarter Equipment: Yes, it requires capital, but modern systems often pay for themselves in a matter of months through reduced energy use.
A Question for the Finance Directors Out There
Here’s something to think about: How often do energy initiatives land on your desk, and how many actually come with a solid ROI case?
Have you started conversations with your operations or engineering team lately about energy savings? If not, why not?
A strategy that combines operational efficiencies with cost savings isn’t just good business—it’s essential for long-term survival.
But let’s hear how others are tackling this challenge. What’s the most effective energy-saving change you’ve implemented in the last year? Or, if you’re just getting started, what’s holding you back?
Let me know your thoughts —it’s a conversation we all need to have.
Comentarios